Teil 1: Translatorische Systeme
In allen Bereichen der Industrie müssen Schüttgüter – auch solche mit schwierigsten Fließeigenschaften – teilweise in vollautomatischem Betrieb gefördert, gelagert und entladen werden. Bei der Auswahl eines Austragssystems ist darauf zu achten, dass die richtige Planung und Bemessung des Silos oder Bunkers unter Berücksichtigung des Fließverhaltens des Schüttgutes eine wesentliche Voraussetzung für einen störungsfreien Betrieb bildet.
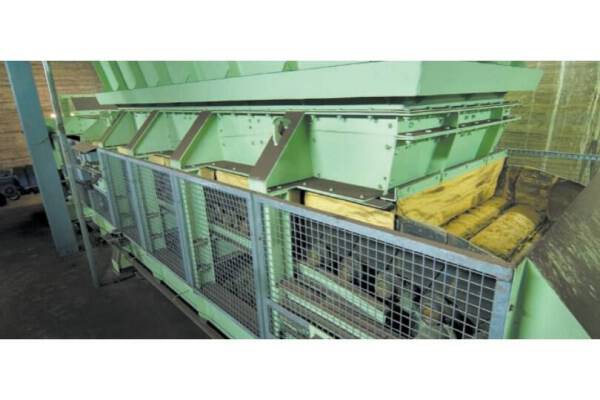
Bunkerabzug Additive
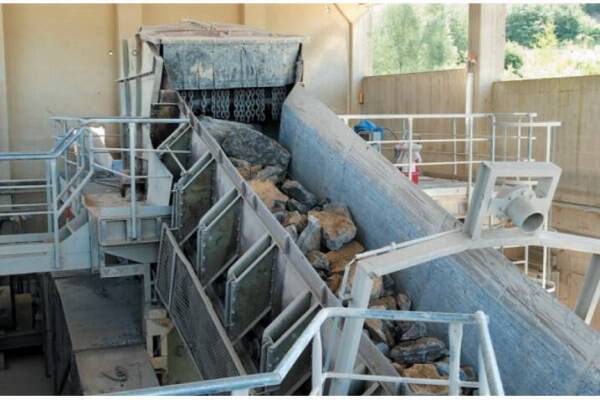
Kippstelle für Kalkstein
Ein noch so gutes Austragsorgan wird unter einem unzureichend dimensionierten Silo oder Bunker keine befriedigenden Ergebnisse erzielen. Darüber hinaus sind aber auch betriebsbedingte und prozesstechnische Anforderungen an das Austragsorgan zu berücksichtigen. Kurzum: Es gibt nicht das multifunktionale Austragsorgan, sondern vielmehr sind Vor- und Nachteile der verschiedenen am Markt angebotenen Systeme im Einzelfall zu bewerten.
In der Richtlinie VDI 2694 „Bunker und Silos, Beschickung, Lagerung und Austrag von Schüttgut“ werden Austragsgeräte und Austragshilfen bekanntermaßen grob klassifiziert und spezifiziert. Dieser Fachbeitrag stellt die gängigsten Austragssysteme vor, zeigt Einsatzbeispiele aus der Praxis und dient als zusätzliche Entscheidungshilfe für die richtige Auswahl.
Für den Austrag von Schüttgütern stehen nach derzeitigem Stand der Technik unterschiedliche Maschinen zur Verfügung. Sie sind für den jeweiligen Einsatzfall konstruiert, in der Praxis erfolgreich getestet und haben sich über die Jahre hervorragend bewährt. Neben einer Übersicht der am Markt vorhandenen Geräte befasst sich der Artikel im wesentlichen mit der Austragsproblematik schwer fließender Schüttgüter.
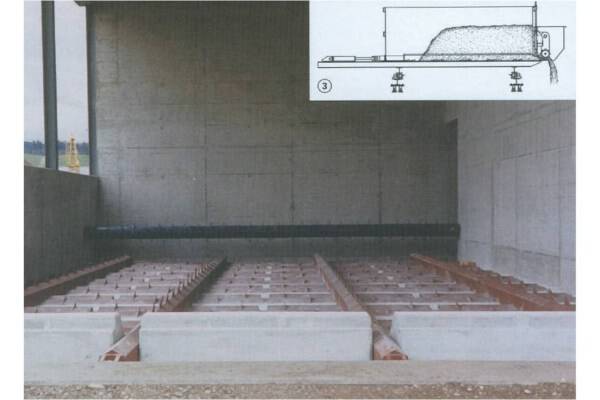
Schubboden mit Austragsschnecke
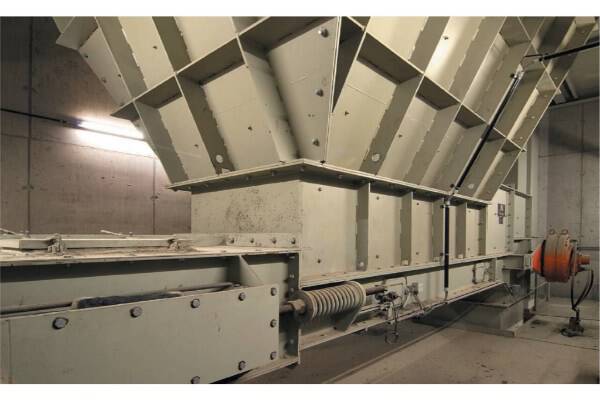
Panzerkettenförderer: Bunkerabzug
Hierbei werden auf die Auswahl der für die Maschine wichtigen Einflussfaktoren eingegangen und unterschiedliche Anwendungsbeispiele vorgestellt.In allen Bereichen der Industrie müssen Schüttgüter – auch solche mit schwierigsten Fließeigenschaften – teilweise in vollautomatischem Betrieb gefördert, gelagert und entladen werden. Bei der Auswahl eines Austragssystems ist darauf zu achten, dass die richtige Planung und Bemessung des Silos oder Bunkers unter Berücksichtigung des Fließverhaltens des Schüttgutes eine wesentliche Voraussetzung für einen störungsfreien Betrieb bildet. Ein noch so gutes Austragsorgan wird unter einem unzureichend dimensionierten Silo oder Bunker keine befriedigenden Ergebnisse erzielen.
Darüber hinaus sind aber auch betriebsbedingte und prozesstechnische Anforderungen an das Austragsorgan zu berücksichtigen. Kurzum: Es gibt nicht das multifunktionale Austragsorgan, sondern vielmehr sind Vor- und Nachteile der verschiedenen am Markt angebotenen Systeme im Einzelfall zu bewerten. In der Richtlinie VDI 2694 „Bunker und Silos, Beschickung, Lagerung und Austrag von Schüttgut“ werden Austragsgeräte und Austragshilfen bekanntermaßen grob klassifiziert und spezifiziert.
Dieser Fachbeitrag stellt die gängigsten Austragssysteme vor, zeigt Einsatzbeispiele aus der Praxis und dient als zusätzliche Entscheidungshilfe für die richtige Auswahl. Für den Austrag von Schüttgütern stehen nach derzeitigem Stand der Technik unterschiedliche Maschinen zur Verfügung. Sie sind für den jeweiligen Einsatzfall konstruiert, in der Praxis erfolgreich getestet und haben sich über die Jahre hervorragend bewährt.
Neben einer Übersicht der am Markt vorhandenen Geräte befasst sich der Artikel im wesentlichen mit der Austragsproblematik schwer fließender Schüttgüter. Hierbei werden auf die Auswahl der für die Maschine wichtigen Einflussfaktoren eingegangen und unterschiedliche Anwendungsbeispiele vorgestellt.
Auswahlkriterien für Austragssysteme
1. Einflussfaktoren
Die Auswahl eines geeigneten Austragssystems richtet sich im Wesentlichen nach drei Kriterien: Schüttguteigenschaften, Silo- oder Bunkerform sowie prozesstechnische Anforderungen. Um eine Maschine richtig auswählen zu können, müssen die Eigenschaften des Fördergutes hinreichend genau bekannt sein.
Wann ein Schüttgut schwer fließend ist, lässt sich zum Beispiel über eine Kennzahl charakterisieren. Fließen bedeutet, dass sich ein Schüttgut aufgrund einer wirkenden Belastung plastisch verformt (etwa beim Bruch einer zuvor verfestigten Schüttgutprobe). Die Fließfähigkeit eines Schüttgutes wird durch die Druckfestigkeit σc im Verhältnis zur Verfestigungsspannung σ1 und gegebenenfalls abhängig von der Lagerzeit als Fließkoeffizient ffc definiert (Abb. 1 und 2).
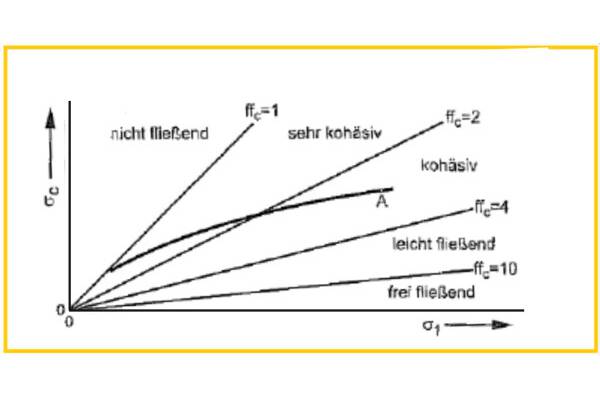
Abb.1 Fließkoeffizient ffc und Bereiche unterschiedlicher Fließfähigkeit
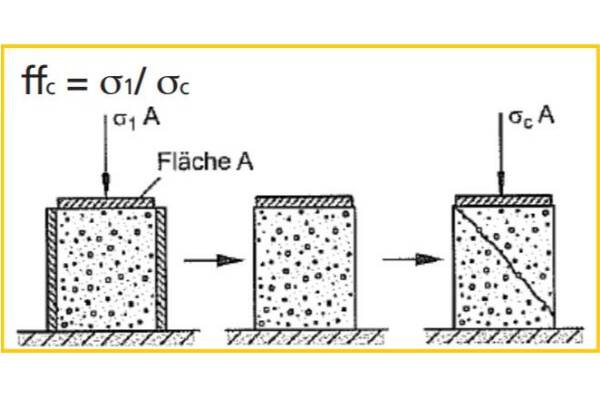
Abb.2 Einachsiger Druckversuch zur Ermittlung der Druckfestigkeit σc
Mit anderen Worten, ein Schüttgut, welches sich durch die Verfestigungsspannung σ1 in hohem Maße verdichten, also verfestigen lässt, wird eine entsprechend hohe Druckspannung σc benötigen, um es zu verformen oder zum Bruch kommen zu lassen. Im Sinne dieser Definition betrachten wir die Schüttgüter mit einem ffc << 2, also solche, die schlecht oder gar nicht fließen. Das Spektrum von zu fördernden Schüttgütern ist allerdings sehr vielfältig und eine Bestimmung des Fließkoeffizienten in der Praxis oft nicht immer sofort möglich. Es liegen aber häufig Förderguteigenschaften oder -kennwerte vor, die eine Einteilung erlauben und daher bei der Auswahl einer Abzugsmaschine berücksichtigt werden müssen.
Hierzu zählen im Wesentlichen die folgenden Fördergutkennwerte:
- Schüttdichte
- Feuchtigkeitsgehalt
- Korngröße
- Korngrößenverteilung
- Temperatur
- Schüttwinkel (innerer Reibungswinkel) und Wandreibungswinkel
- Zusatzinformationen über Fließeigenschaften, Staubanteil, Abrasivität und Korrosionsverhalten
- Zeitstandverhalten.
Bei Letzterem ändern sich teilweise die vorgenannten Materialparameter mit zunehmender Lagerung, was die Auslegung nicht gerade einfach macht. Erschwerend kommen weitere Abhängigkeiten hinzu. So können jahreszeitliche Schwankungen (zum Beispiel des Feuchtigkeitsgehaltes) zu Änderungen des Materialverhaltens führen. In manchen Fällen sind den Betreibern selbst die einfach ermittelbaren Materialeigenschaften nur unzureichend bekannt (etwa bei noch nicht erschlossenen Abbaugebieten oder fremd angeliefertem Material).
Zusätzlich gibt es noch Anwendungsfälle, in denen unterschiedliche Fördergüter oder eine Mischung von Fördergütern über ein und dieselbe Maschine gefördert werden müssen. Für einige „Standard-Schüttgüter“ mit gutmütigen Fließeigenschaften sind die zur Auslegung einer Abzugsmaschine wesentlichen Kenngrößen meistens bekannt. Schwieriger wird es bei problematischen Schüttgütern mit schlechten Fließeigenschaften oder sich dynamisch ändernden Kenngrößen. Hierbei ist eine experimentelle Untersuchung des Materials im Schüttgutlabor zur Ermittlung der Materialparameter zwingend erforderlich. Aus der Summe aller bisher durchgeführten Laboruntersuchungen besteht im Hause Aumund Fördertechnik GmbH eine Schüttgutbibliothek mit Fördergutkennwerten von mehr als 700 verschiedenen Materialien.
Bauform von Bunkern
Ein weiterer wesentlicher Einflussfaktor ist die Bauform von Bunkern, Silos oder Kippstellen und des Förderers selbst. Bekanntermaßen entstehen durch eine vorgegebene Silo-Geometrie unterschiedliche Fließprofile. Schlechte Fließfähigkeit im Trichter bedeutet, dass es zu Auslaufstörungen aufgrund von Brückenbildung kommt. Durch die Berücksichtigung der Materialparameter bei der konstruktiven Auslegung der Bunker- oder Silo-Geometrien wie Wandneigungswinkel und Auslaufquerschnitt werden diese unerwünschten Effekte eliminiert. Hier wird ersichtlich, wie wichtig eine möglichst genaue Bestimmung der Fördergutkennwerte ist. Unsicherheiten können in der Praxis zu Problemen führen.
Bei der Entscheidung, welche Austragsmaschine nun letztendlich zum Einsatz kommt, spielen nicht nur die Schüttgutparameter, sondern auch eventuelle örtliche Voraussetzungen sowie Einbau- und Platzverhältnisse eine Rolle. Abbildung 3 zeigt die gebräuchlichsten Silo- und Bunkerformen. Am häufigsten findet man in der Praxis axialsymmetrische Silos oder Bunker mit konischem Trichter (siehe Schaubild 3a) oder so genannte Schlitzbunker mit keilförmigem Trichter (siehe Schaubild 3b,c,d).
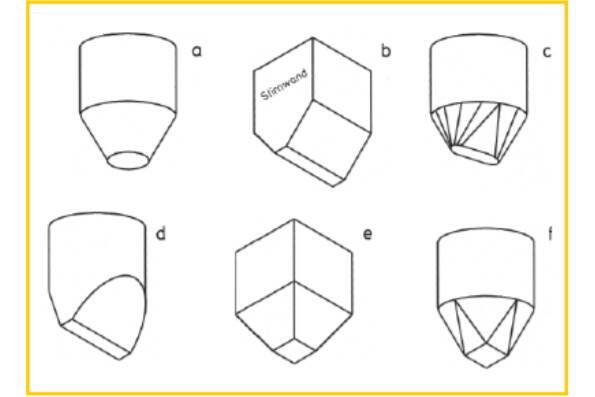
Abb. 3 Gebräuchlichste Silo- und Bunkerformen
In der Regel sind auch prozesstechnische Anforderungen zu berücksichtigen, die auf die Auswahl des Austragsorgans wesentlichen Einfluss haben. Einige Kriterien oder Bedingungen, die zu klären sind, können sein:
- Welche Massenströme sind zu fördern?
- Welche Lagerkapazitäten werden gefordert?
- Konstanter oder regelbarer/dosierter Austragsmassenstrom?
- Restlosentleerung (zum Beispiel bei ATEX)?
- Gekapselt oder offen (zum Beispiel bei ATEX oder Unterdrucksystemen)?
- Ortsfest oder mobil?
- Verfügbarkeit (Abwägung Investitionskosten/Betriebskosten)?
- Dynamische Beanspruchung (zum Beispiel Stoßbelastung bei Kippstellen)?
- Häufi ges Anfahren mit vollem Bunker oder Silo?
- Entleerungskonzept (First in, First out = FiFo). Das Entleerungskonzept kann nicht nur aus prozesstechnischen Gründen wichtig sein, sondern ist auch für den sicheren Austrag von schwer fließenden Schüttgütern von grundsätzlicher Bedeutung. „First in, First out” bedeutet, dass das Schüttgut, welches als erstes ins Silo gefüllt wurde, auch als erstes wieder ausgetragen wird. Damit werden lange Verweilzeiten verhindert, was unter Berücksichtigung der zuvor genannten Schüttguteigenschaften von entscheidendem Vorteil sein kann.
2. Übersicht der wichtigsten Austragsvorrichtungen
Bei der Auswahl eines Austragsgerätes ist immer grundsätzlich darauf zu achten, dass sich keine toten Zonen (Kernfluss) im Silo bilden. Grundsätzlich unterscheidet man translatorische und rotatorische Systeme. Translatorische Austragssysteme sind zum Beispiel Gurt- und Schneckenförderer, Plattenbänder, Trog- und Panzerkettenförderer, Schwingrinne, Schneckenund Schubboden. Rotatorische Austragssysteme sind beispielsweise Räumschnecke und -kratzer, Drehteller, Drehkratzer beziehungsweise Räumarm, Räum- und Kreisräumwagen. Austragssysteme für große Querschnitte sind zudem Panzerkettenförderer, Plattenbänder, Schnecken- und Drehbalkenboden. Einen genaueren Überblick ermöglicht die VDI 269 „Bunker und Silos, Beschickung, Lagerung und Austrag von Schüttgut“. Austragssysteme, welche nicht nach dem FiFo-Prinzip arbeiten (zum Beispiel das im Silo gelagerte Schüttgut von oben ausräumen / Stichwort Absetzer oder Euro-Silo), sollen hier nicht weiter betrachtet werden.
3. Auswahlmatrix
Die Auswahlmatrix (Tabelle 1) soll einen ersten Überblick über die Eignung verschiedener Austragsorgane geben, basierend auf den Betriebserfahrungen im Hause Aumund.
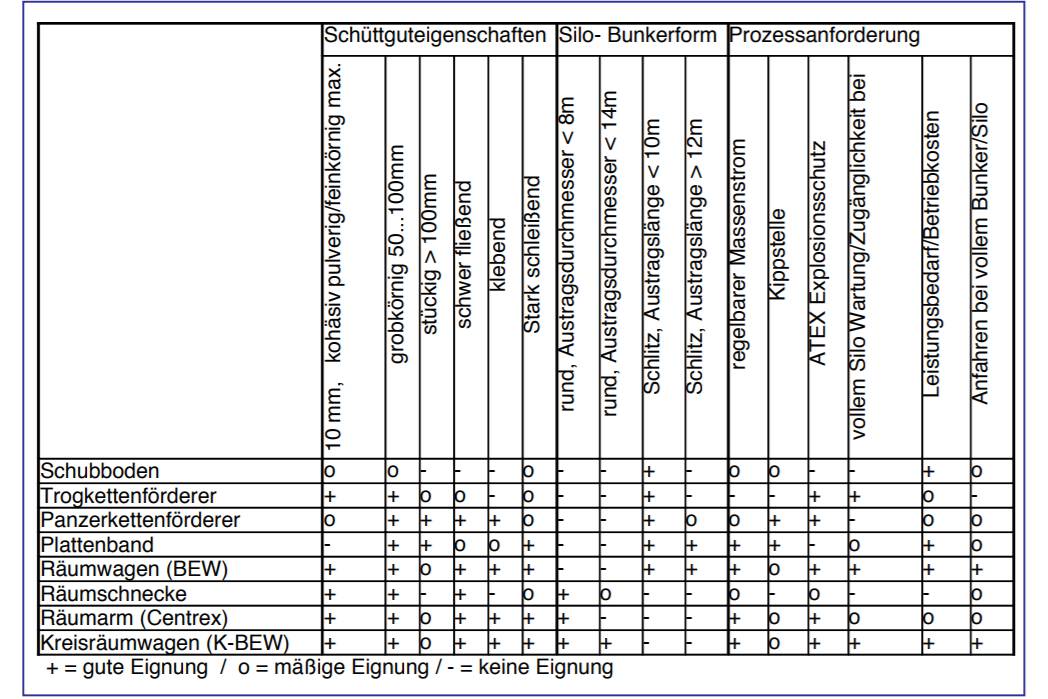
Tabelle-1 Auswahlmatrix verschiedener Austragsorgane
1. Austrag mit einem Trogkettenförderer
Aufgrund ihrer kompakten und geschlossenen Bauweise sowie der Möglichkeit, mehrere Abwurfpunkte zu realisieren, sind Trogkettenförderer (TKF) im SchüttgutHandling sehr beliebt. TKF gibt es als Ein- oder Zweistrangförderer. Als Zugträger werden geschmiedete Gabellaschenketten eingesetzt. In druckstoßfester Ausführung eignen sich TKF sogar zum Transport entzündlicher Materialien wie zum Beispiel Kohle. TKF wurden als Stetigförderer für kontinuierliche Massenströme überwiegend für staubige Fördergüter konzipiert, worauf sich die international gebräuchliche Bezeichnung „EnMasse Conveyor“ ableitet.
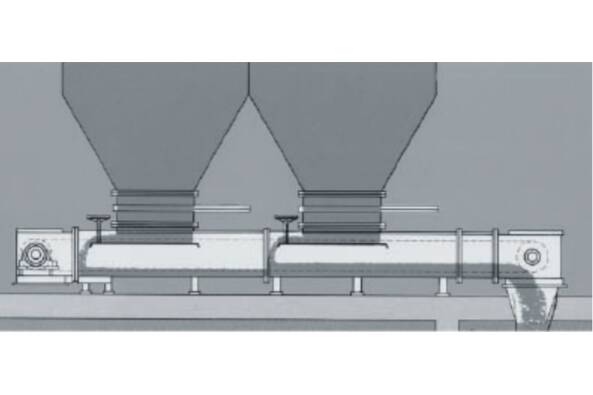
Abb.4 TKF mit Zwischenboden
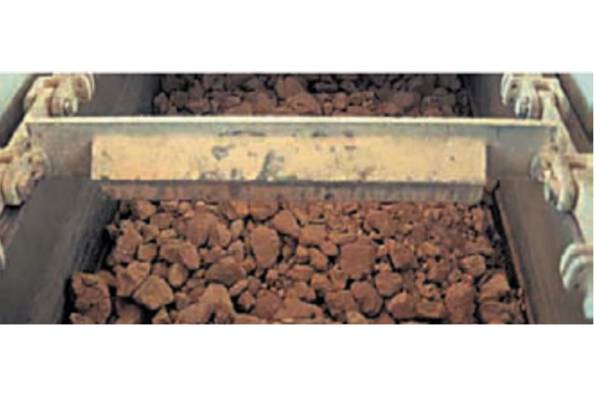
Abb.5 EnMasse Conveyor-Prinzip
Das Förderprinzip beruht auf der Tatsache, dass eine gleichmäßige Schichthöhe als Paket zwischen den Mitnehmern „ruht“, wodurch keine Relativbewegung zwischen Kette und Schüttgut auftritt und der Verschleiß sich für Kette und Mitnehmer in Grenzen hält (Abb 5). Als Kratzer (= Umwälzung des Materials vor dem Mitnehmer) ist der TKF daher nur bedingt einsetzbar. Zum Abzug aus Bunkern und Silos muss ein Zwischenboden eingebaut werden, um eine Überschüttung zu vermeiden (Abb. 4). Für stückige (Korngrößen > 100 mm) oder klebrige Schüttgüter sind Trogkettenförderer grundsätzlich nicht geeignet, was gleichzeitig die Verwendung als Austragsorgan für schwierige Schüttgüter sehr stark einschränkt. Als Abzugsförderer finden TKF vorzugsweise für Kohle Verwendung. Die maximale Auslaufbreite beträgt 1.000 mm. Darüber hinaus sind Panzerkettenförderer als Dreioder Vierstranglösung einzusetzen, deren Ketten und Mitnehmer entsprechend stärker ausgeführt sind und sich somit auch höhere Abzugskräfte ohne Gefahr von Schäden realisieren lassen.baut werden, um eine Überschüttung zu vermeiden (Abb. 4). Für stückige (Korngrößen > 100 mm) oder klebrige Schüttgüter sind Trogkettenförderer grundsätzlich nicht geeignet, was gleichzeitig die Verwendung als Austragsorgan für schwierige Schüttgüter sehr stark einschränkt. Als Abzugsförderer finden TKF vorzugsweise für Kohle Verwendung. Die maximale Auslaufbreite beträgt 1.000 mm. Darüber hinaus sind Panzerkettenförderer als Dreioder Vierstranglösung einzusetzen, deren Ketten und Mitnehmer entsprechend stärker ausgeführt sind und sich somit auch höhere Abzugskräfte ohne Gefahr von Schäden realisieren lassen.
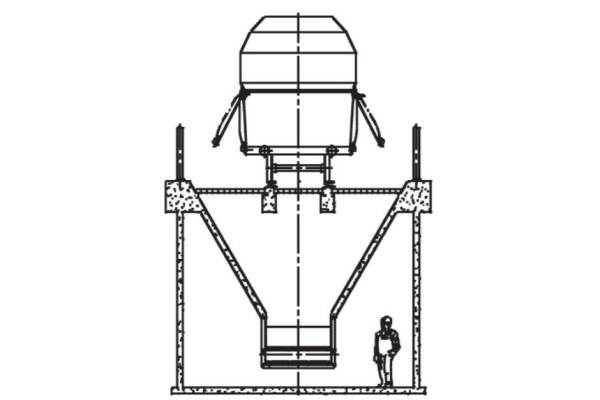
Abb. 6 Bunkerabzug mit Typ PKF
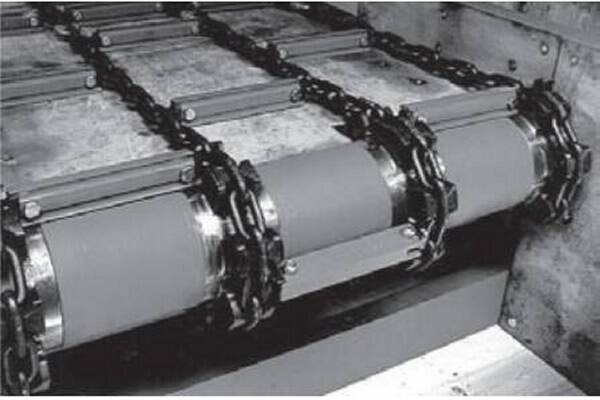
Abb. 7 Panzerkettenförderer PKF
2. Austrag mit einem Panzerkettenförderer
Der Panzerkettenförderer Typ PKF zeichnet sich durch die geringe Bauhöhe und den dichten Anschluss an die Bunkerkonstruktion aus. Auffällig ist außerdem, dass aufgrund der stabilen Ausführung kein Entlastungskegel erforderlich ist. Dadurch ist der gesamte Bunkerquerschnitt nutzbar (Abb. 6 und 7). Das Zugelement der Panzerkettenförderer besteht aus Rundstahlketten, die je nach Einsatzfall in vergüteter oder gehärteter Ausführung gewählt werden. Durch die Kombination von zwei bis fünf Kettensträngen mit den zugehörigen Kratzern können Trogbreiten von 600 bis 2.600 mm realisiert werden. Insbesondere bei klebrigen Schüttgütern können entsprechend große Auslaufbreiten im Bunker erreicht werden, um Fließprobleme zu vermeiden. Ketten und Kratzer bewegen das Fördergut im Obertrum auf einer verschleißgeschützt ausgeführten Bodenplatte (Abb. 7). Von ihnen abfallendes Gut wird im leeren Untertrum zurückgefördert und dem Obertrum wieder zugeführt. So sind zusätzliche Reinigungskratzer nicht erforderlich. Der Panzerkettenförderer wird vorzugsweise als Bunkerabzug, für Kalksteinschotter oder für klebende Rohmaterialien wie Kreide, Gips, Mergel, Ton oder feuchte Rohkohle eingesetzt. Korngrößen bis 200 mm (Einzelstücke bis 250 mm) lassen sich problemlos fördern. Gerade klebendes Material neigt dazu, über den Abwurf hinaus zu wandern, um dann als Kuchenstück abzubrechen. Dies führt dann dazu, dass auf dem nachgeschalteten Band ungleichmäßig verteilte Haufen liegen. Um einen gleichmäßigen Materialfluss zu erreichen, kann man für schwer fließende Schüttgüter im Bereich der Antriebstrommel eine Haspelwelle vorsehen, die den Fördergutstrom auflockert. Die Haspelwelle arbeitet je nach aufbau des Materials und seinen Fließeigenschaften. Für leicht fließende Schüttgüter mit Korngrößen von 0 bis 0 mm ist eine Mindestaufbau des Materials und seinen Fließeigenschaften. Für leicht fließende Schüttgüter mit Korngrößen von 0 bis 0 mm ist eine Mindestschichthöhe von 00 bis 00 mm erforderlich. Bei schwer fließenden Schüttgütern müssen Schichthöhen von wenigstens 600 bis 00 mm eingestellt werden, um den Bunkeraustrag zu gewährleisten. Bei der Auslegung der Antriebsleistungen wird vorzugsweise eine Geschwindigkeit von 0,1 m/s für die Nennförderleistung gewählt. Entsprechend gering ist auch die Drehzahl der Antriebswelle, so dass hoch untergesetzte Getriebe verwendet werden müssen. Besonders geeignet sind deshalb Planetengetriebe oder hydraulische Antriebseinheiten.

Abb. 8 Kurzzellenband Typ KZB
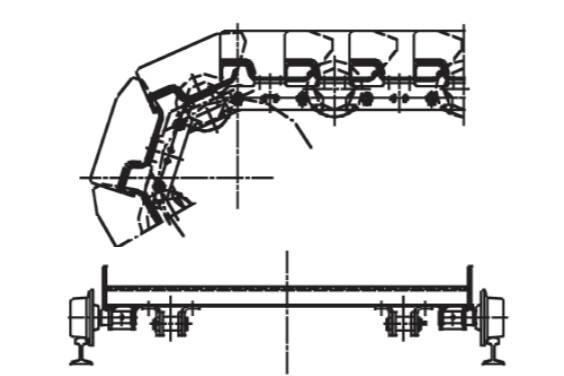
Abb.9 Kurzzellenband – Plattenprofil
3. Bunkeraustrag mit einem Plattenband
Plattenbänder gibt es in unterschiedlichen Ausführungen. Sie sind insbesondere bei schweren Betriebsbedingungen einsetzbar und eignen sich unter anderem für stückige beziehungsweise kantige, stark abrasive und heiße Schüttgüter. Das Kurzzellenband (KZB) in Abbildung wird vorzugsweise unter längeren Bunkern eingesetzt und fördert zum Beispiel Rohkohle, Koks und Zementklinker. Das besondere Profi l der Kurzzelle hat ein hohes Widerstandsmoment und ist damit in der Lage, bei kleinem Eigengewicht relativ hohe Bunkerlasten bei geringer Durchbiegung aufzunehmen (Abb. und 9). Der Kostenvorteil dieser Lösung beruht auf der ausschließlichen Verwendung von Standardbaugruppen, die in Serie für die Zementindustrie gefertigt werden. Der Einsatz fi ndet seine Grenzen nicht in der Plattenbelastung, sondern in der Belastung der Standardlaufrollen. Stärkere Laufrollen würden den Serieneffekt zunichte machen. Zur Reduzierung der Plattenbelastung und der Abzugskräfte empfi ehlt sich der Einsatz eines Druckentlastungssattels im Bunker (Abb. 10 und 11).
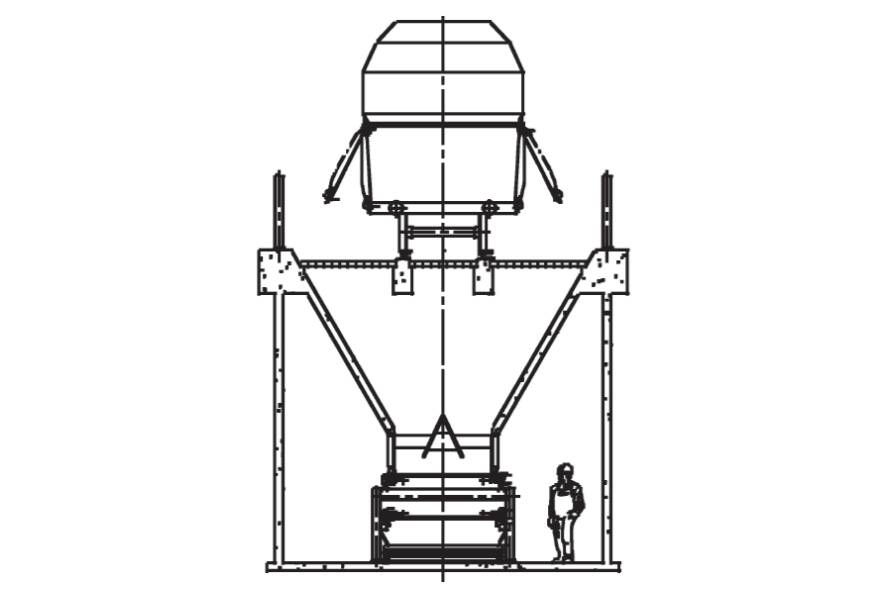
Abb.10 Bunkerabzug mit Kurzzellenband Typ KZB
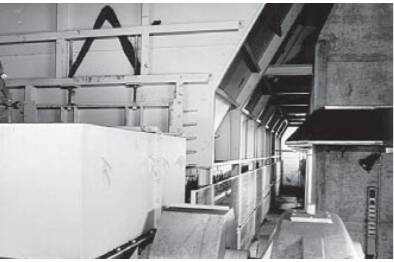
Abb.11 Bunker mit Kurzzellenband Typ KZB
Als Verschleißschutz können die Kanten mit Schutzkappen ausgerüstet werden (Abb. 9). Das Buckelplattenband (BPB) wird vorzugsweise für klebende Rohmaterialien wie Gips, Anhydrit, Ton und Mergel-Tongemisch eingesetzt. Seine Bauart ist mit buckelförmigen Platten ausgerüstet, die im Bereich des Kettenrades (Abwurfbereich) eine kreisförmige Oberfläche bilden (Abb. 12 und 13). Hier kann ein fester Abstreifer angeordnet werden, der klebendes Material von den Platten trennt. Eine regelbare Antriebseinheit in Verbindung mit einer Bandwaage ermöglicht den dosierten Abzug für die Beschickung von Mahlanlagen. Schwere Buckelplattenbänder (BPB-S und BPB-SF) werden vorzugsweise unter Kippstellen angeordnet und transportieren ungebrochene Rohmaterialien wie zum Beispiel Kalkstein und Gips mit Kantenlängen bis zu 1.000 mm zu der Brecheranlage. Je nach Korngröße, Durchsatzleistung und Dimensionierung des Trichters ergeben sich die Stärken der Bandplatten.-SF. stehen je nach Erfordernis Platten von 20 bis 80 mm Stärke und einer Breite von maximal 3.000 mm zur Verfügung. Entsprechend kommen Raupenketten mit Bruchlasten bis zu 2 x 3.600 kN (360 t) zum Einsatz.
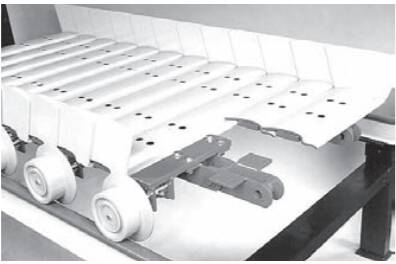
Abb.12 Buckelplattenband Typ BPB
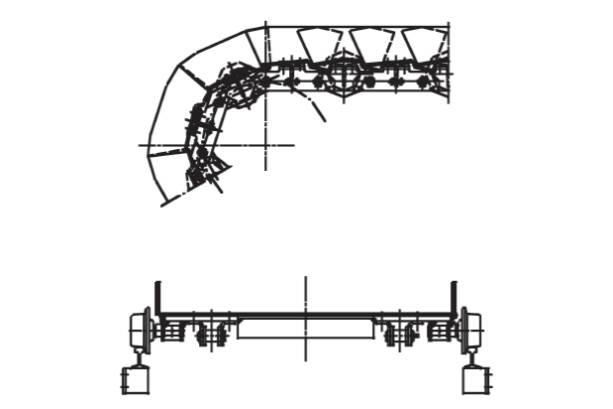
Abb.13 Buckelplattenband – Buckelform
Durch die mechanische Bearbeitung der Überlappungskanten und gekröpfte Seitenborde wird die Dichtigkeit der Platten untereinander sichergestellt. Für die Aufnahme der Vertikalkräfte stehen zwei Laufrollenkonzepte zur Verfügung: Typ BPB-S mit außen liegenden mitfahrenden, kugelgelagerten Laufrollen und schweren Feldbahnschienen (Abb.14). Abbildung 15 zeigt die Verstärkung des Aufgabebereichs durch Prallträger. Typ BPB-SF mit schweren feststehenden, gleitgelagerten Laufrollen aus dem Raupenfahrwerksprogramm, angeordnet unter den Raupenketten (Abb. 16 und 17). Unter dem Plattenband können Reinigungskratzer eingesetzt werden, um abfallendes Rieselgut ohne manuellen Reinigungsaufwand zu entfernen.
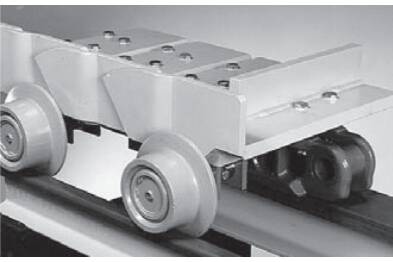
Abb.14 Buckelplattenband Typ BPB-S
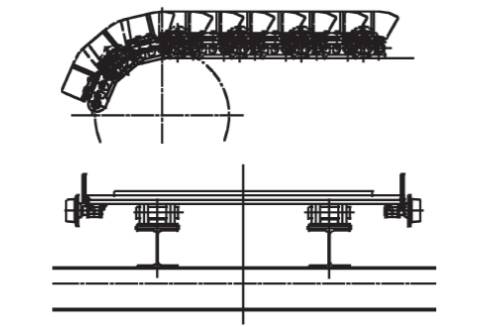
Abb.15 Typ BPB-S mit Laufrollen und Prallträger
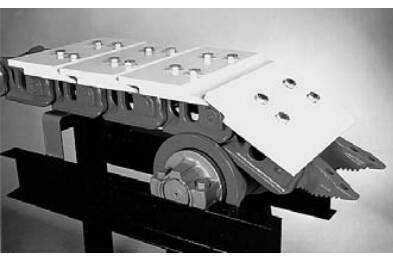
Abb.16 Buckelplattenband Typ BPB-SF
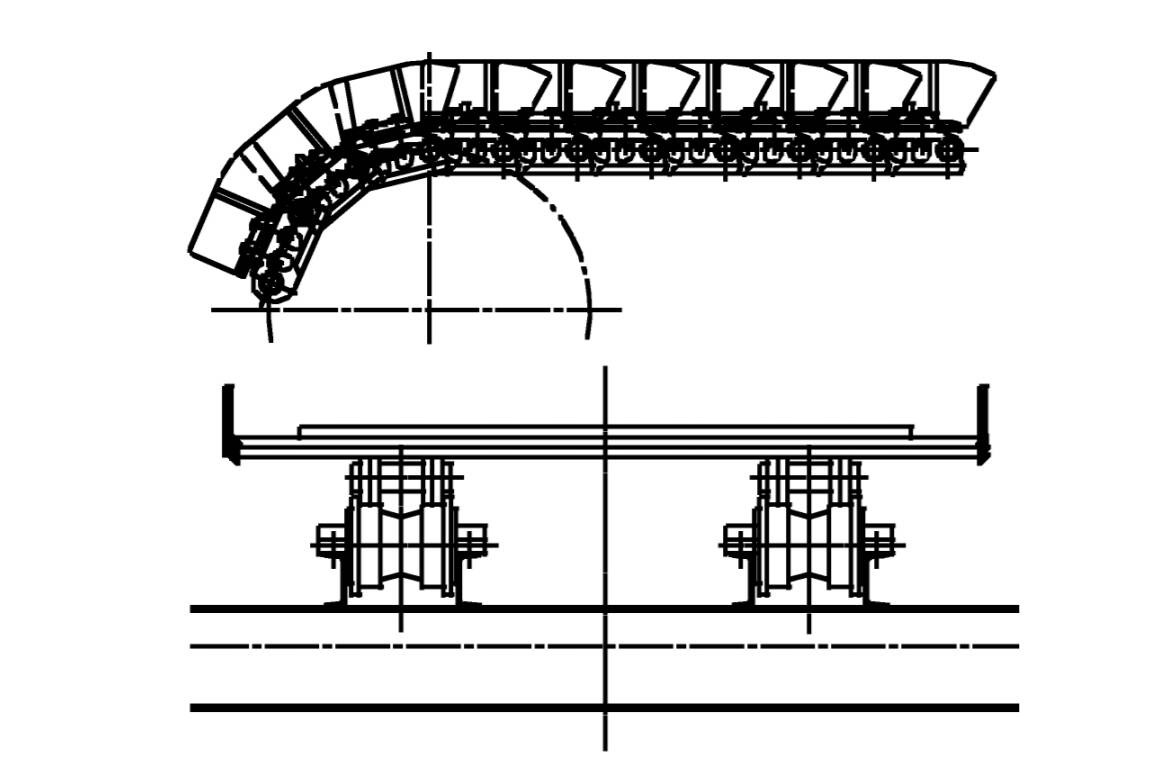
Abb.17 Buckelplattenband mit festen Laufrollen
3. Austrag mit Gurtförderern
Für leichtere Anwendungen (etwa unter kleinen Vorratsbehältern mit entsprechend geringen vertikalen Bunkerlasten) sind auch Gurtförderer einsetzbar, welche zum Beispiel unterhalb des Auslaufes über einen Gleittisch oder enggesetzten Rollenstühlen laufen. Allerdings ist der manchmal nicht unerhebliche Verschleiß des Gurtes zu berücksichtigen. Als eine interessante Alternative – insbesondere wenn mobile Systeme wie zum Beispiel LKW-Kippstellen mit Lagerkapazitäten bis zu 40 t gefordert sind – sei an dieser Stelle auf den „Samson Feeder“ hingewiesen werden. Er ähnelt vom Grundprinzip eher einem Plattenband, da eine Kette die Zugkraft übernimmt und Laufrollen über Quertraversen, auf denen der Gurt befestigt wird, die vertikalen Lasten aufnehmen (Abb. 18). Der Gurt wird somit als reines Tragorgan genutzt, auf dem das Schüttgut ruhend und damit verschleißarm gefördert wird. Gleichzeitig lassen sich mit diesem System Abzugsbreiten bis zu 3.000 mm realisieren, was insbesondere bei schwer fließenden Schüttgütern von Bedeutung ist. Die glatte Oberfläche des Gurtes ist zudem mittels Abstreifer leicht zu reinigen. Er eignet sich sowohl für feinkörniges als auch grobkörniges Schüttgut bis 350 mm und Förderleistungen bis 600 m³/h. Für extrem stückige, abrasive oder heiße Schüttgüter sind solche Systeme aber nicht geeignet. Ein besonderer Vorteil liegt in der „Überflur-Aufstellung“ bei Kippstellen, das heißt auf teuren Tiefbau/Betonbau kann verzichtet werden (Abb. 19).
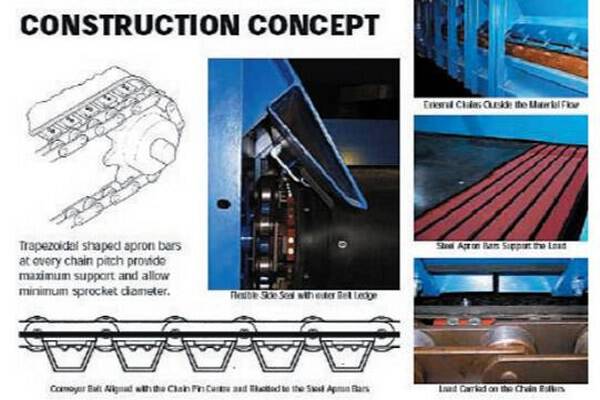
Abb.18 Konstruktionsprinzip Samson Feeder
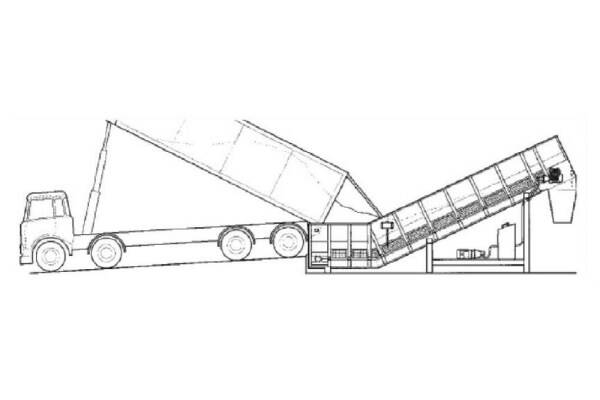
Abb.19 Beispiel Kippstelle mit Samson
5. Austrag mit Schubboden
Schubböden eignen sich vorwiegend für den Austrag von fließfähigen oder leicht kohäsiven Schüttgütern für kleine bis mittlere Korngrößen bis zirka 50 mm. Sie finden überwiegend in der Abfallentsorgung oder -verwertung Anwendung. Schubböden werden in Silos mit flachen Böden eingesetzt und bestehen aus mehreren nebeneinander liegenden Schubelementen, welche durch Schubstangen über Hydraulikzylinder hin- und herbewegt werden (Abb. 20). Problematisch bei schwer fließenden Schüttgütern ist, dass sich das Schüttgut an der Stirnwandseite ohne Auslauf verdichtet, was unter anderem zu steigenden Antriebskräften führen kann. Für schwer fließende Fördergüter also keine ideale Lösung. Es sei an dieser Stelle aber der Vollständigkeit halber erwähnt, dass seitens Aumund keine Betriebserfahrungen für den Einsatz von Schubböden mit schwer fließenden Schüttgütern vorliegen, da die vorhandenen Siloböden überwiegend für Holzschnitzel und Austragsleistung bis 150 m³/h eingesetzt wurden.
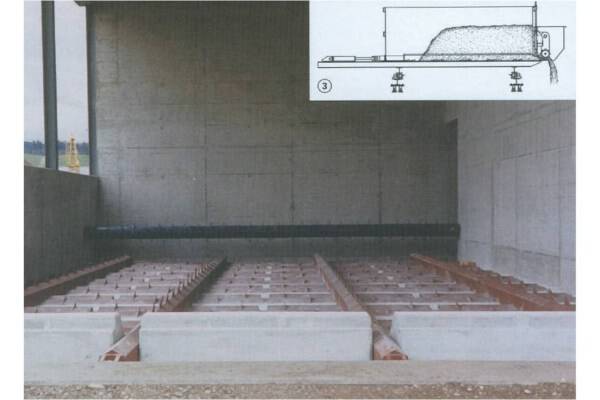
Schubboden mit Austragsschnecke